Wir erklären, wie LEWA Attendorn höchste Qualitätsansprüche, geringe Stückzahlen und eine niedrige TCO im Automobilbau zusammenbringt.
Die Kundenanforderung:
Konzeptentwicklung eines Produktionssystems für das Heck eines hybriden Super-Sportwagens mit höchsten Qualitätsansprüchen, jedoch in geringer Stückzahl.
Applikationsprozesse:
- Stanznieten (350 Stück je Baugruppe)
- MIG-Schweißen (Gesamtlänge 2.480 mm)
- Kamerageführtes setzen von Blindnietbolzen (48 Stück je Baugruppe)
- Klebeauftrag einschl. Kamerakontrolle (Gesamtlänge 8.100 mm)
- Dichtmittelauftrag (Gesamtlänge 7.650 mm)
Sind auf mehrere Produktlebenszyklen und somit auf einen „ReUse“-Fall ausgelegt
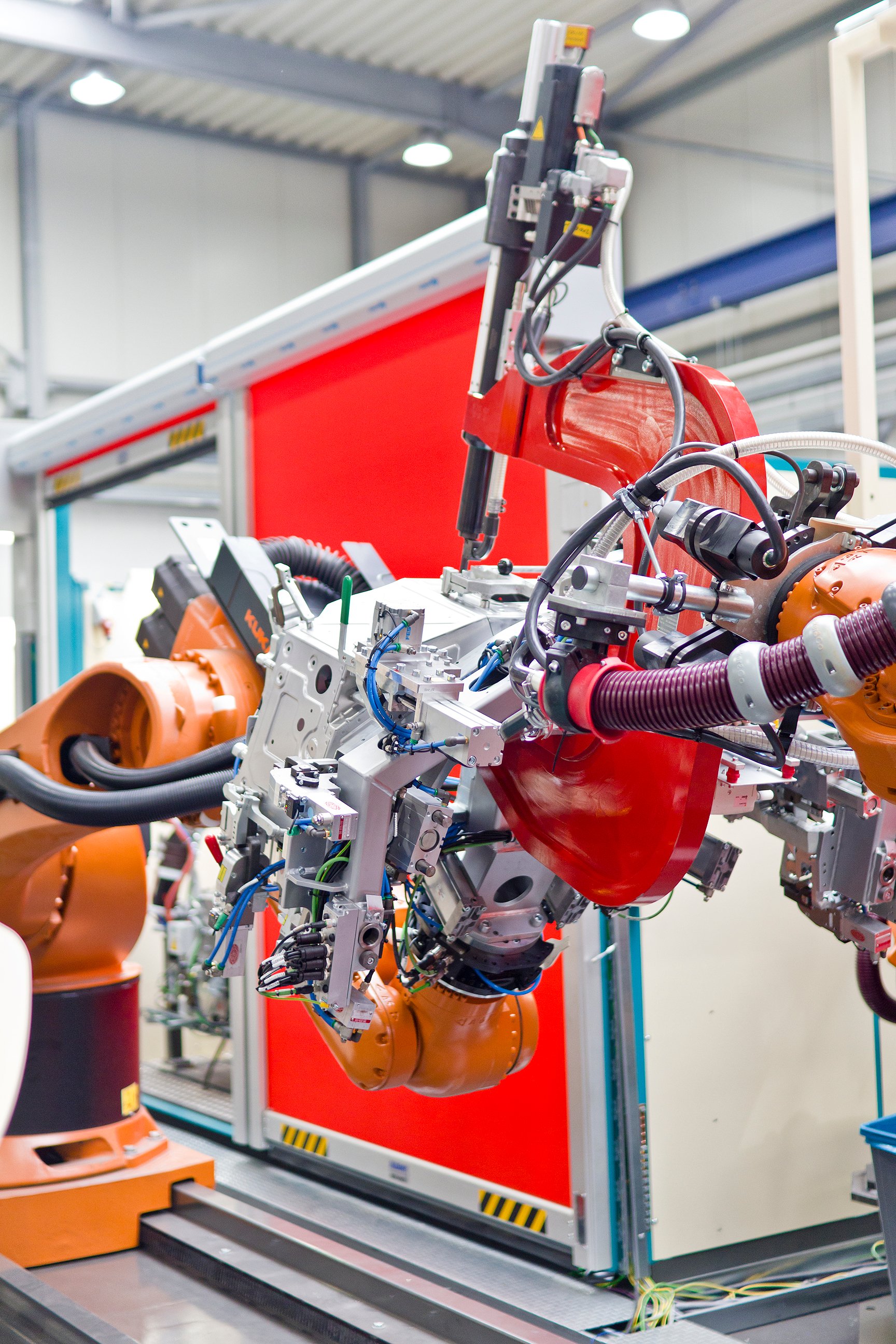
Unsere Lösung:
Aufbau einer hochautomatisierten Fertigungslinie aus einzelnen, standardisierten Produktionsmodulen
- Minimaler Werkzeug und Applikationseinsatz durch „Part to the Tool“-Einsatz
- Variable Vorrichtungs- und Greifertechnik einschließlich automatisiertem Rüstvorgang für ein Derivat
- Servomotorischer Stanzniettechnik mit automatischen Werkzeugwechslern
- Automatisierter Klebeauftrag und Dichtmittelauftrag mit anschließender Überwachung mittels industrieller Bildverarbeitung
- Kamerageführtes Setzen von Blindnietbolzen
- Teilekennzeichnung und Dokumentation der Produktionsdaten
- Ausschleusen der Baugruppen im Sonderladungsträger
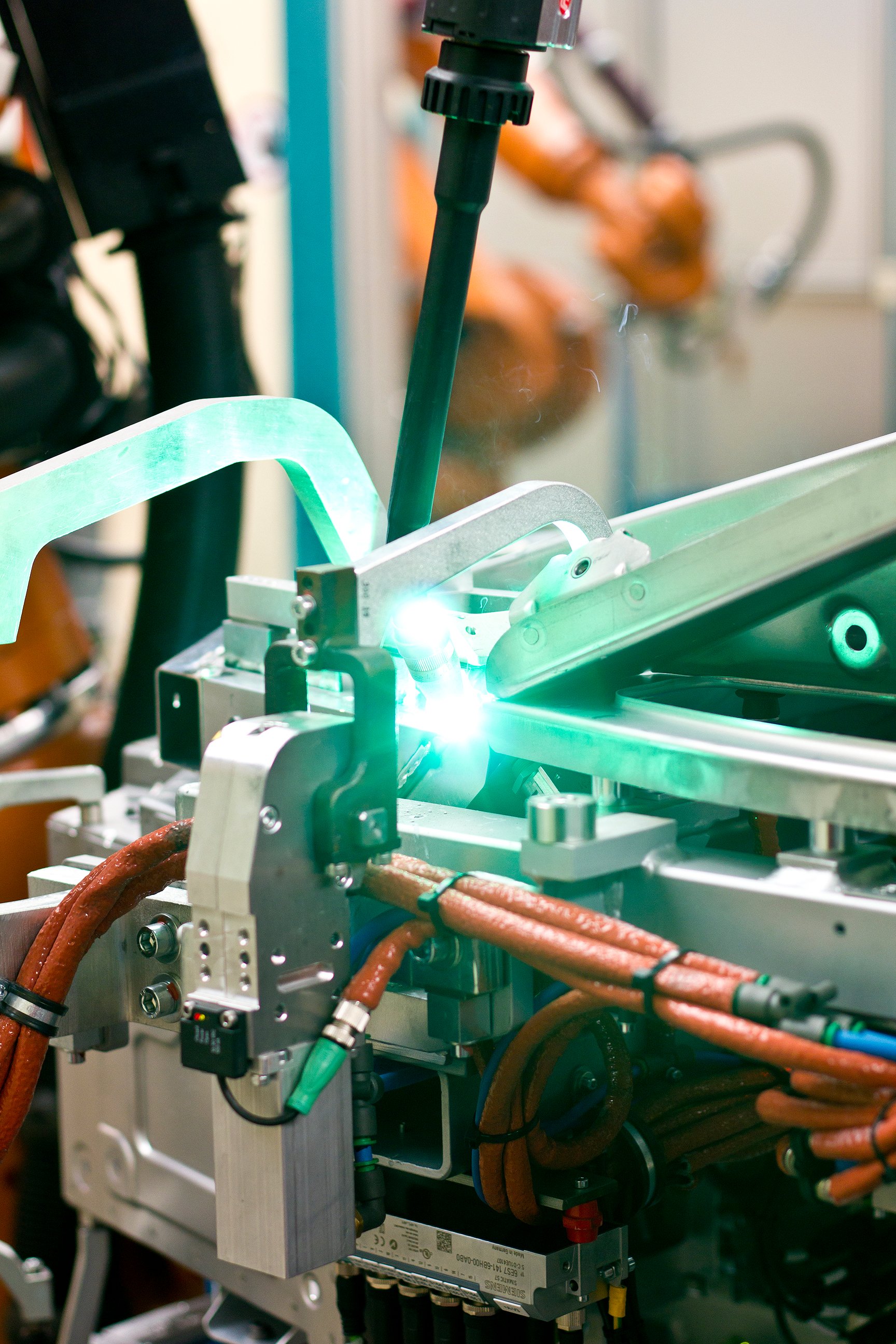
Der Kundenmehrwert:
Kostenoptimierte Module, die bei der LEWA Attendorn ausgetestet und sofort nach Lieferung ihre Arbeit aufnehmen.
- Maximal flexibel und über die eingesetzte Werkzeugtechnik auf andere Produkte rüstfähig
- Modulbauweise macht mobil und lässt somit sehr schnell innerbetrieblich oder Gruppenweit Verlagerungen zu
- Der „ReUse“-Fall wurde bei der Konzeptentwicklung gleich mitgedacht
- Hochautomatisierte Lösung für gleichbleibend hohe Qualität und gleichbleibend hohe Produktivität
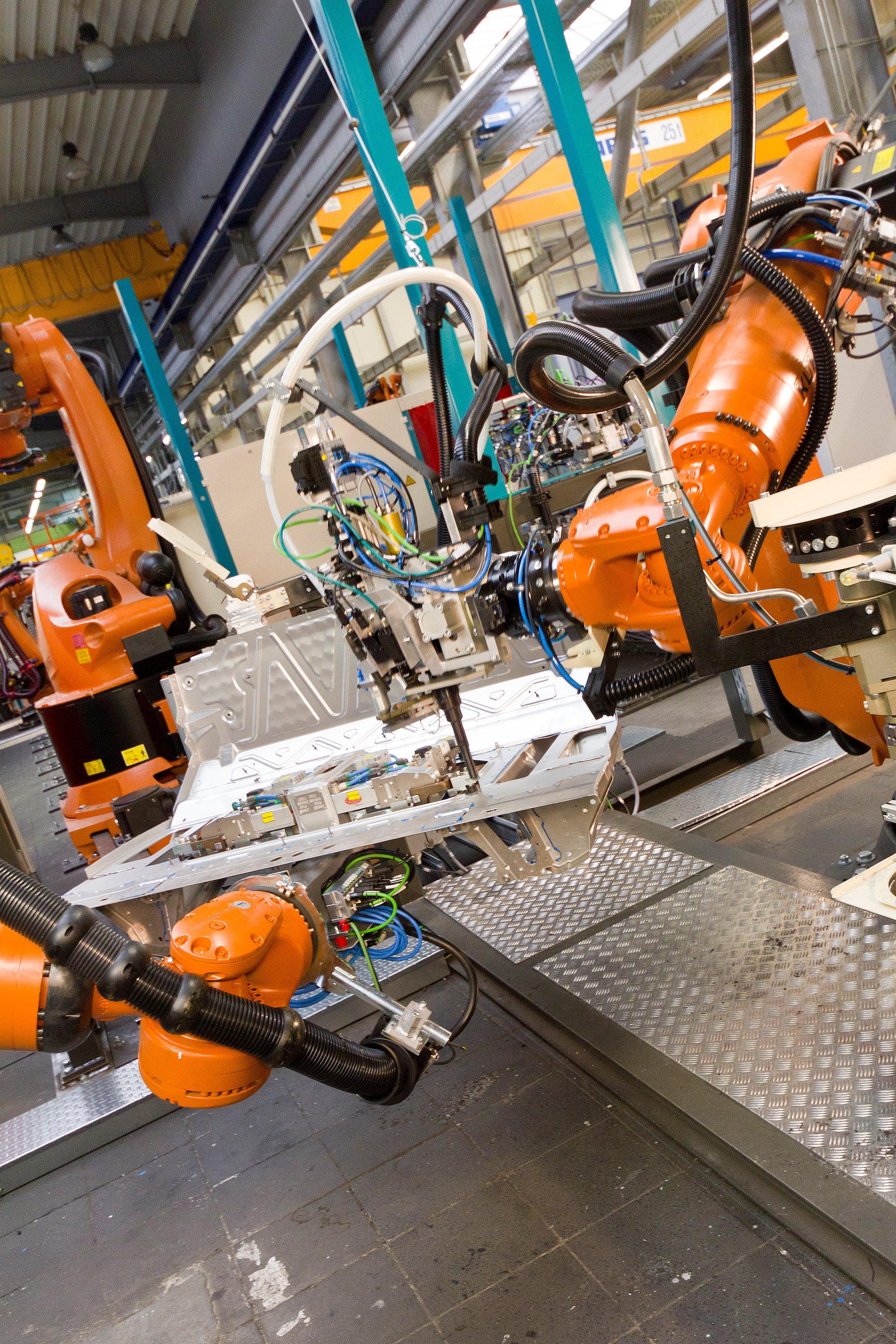
Sie möchten mehr über die LEWA Attendorn erfahren? – Gerne!
Vereinbaren Sie unverbindlich einen Ersttermin und treten Sie mit uns in Kontakt.
