We explain how LEWA Attendorn provides its customer with a production system for the manufacture of thick-walled safety cabinets for the subsequent installation of drive and control components.
Customer requirement:
Manufacture of thick-walled safety cabinets in a wide variety and with the highest requirements for welded joints and geometric dimensions for the subsequent installation of drive and control components.
Application processes:
- Mechanical processing (milling/drilling/tapping) of the individual side elements
- MIG welding (total length up to 12,480 mm)
- Grinding - paintable overgrinding of welds
Our solution:
Construction of a highly automated production line.
- Design and construction of a CNC-controlled clamping device for max. flexibility of the products
- Flexible fixture and gripping technology including an automated set up process for component variations.
- Fully automated manufacturing process: from picking up the individual parts to tacking and welding out the components with subsequent overgrinding of the weld seams and transfer to the paint line.
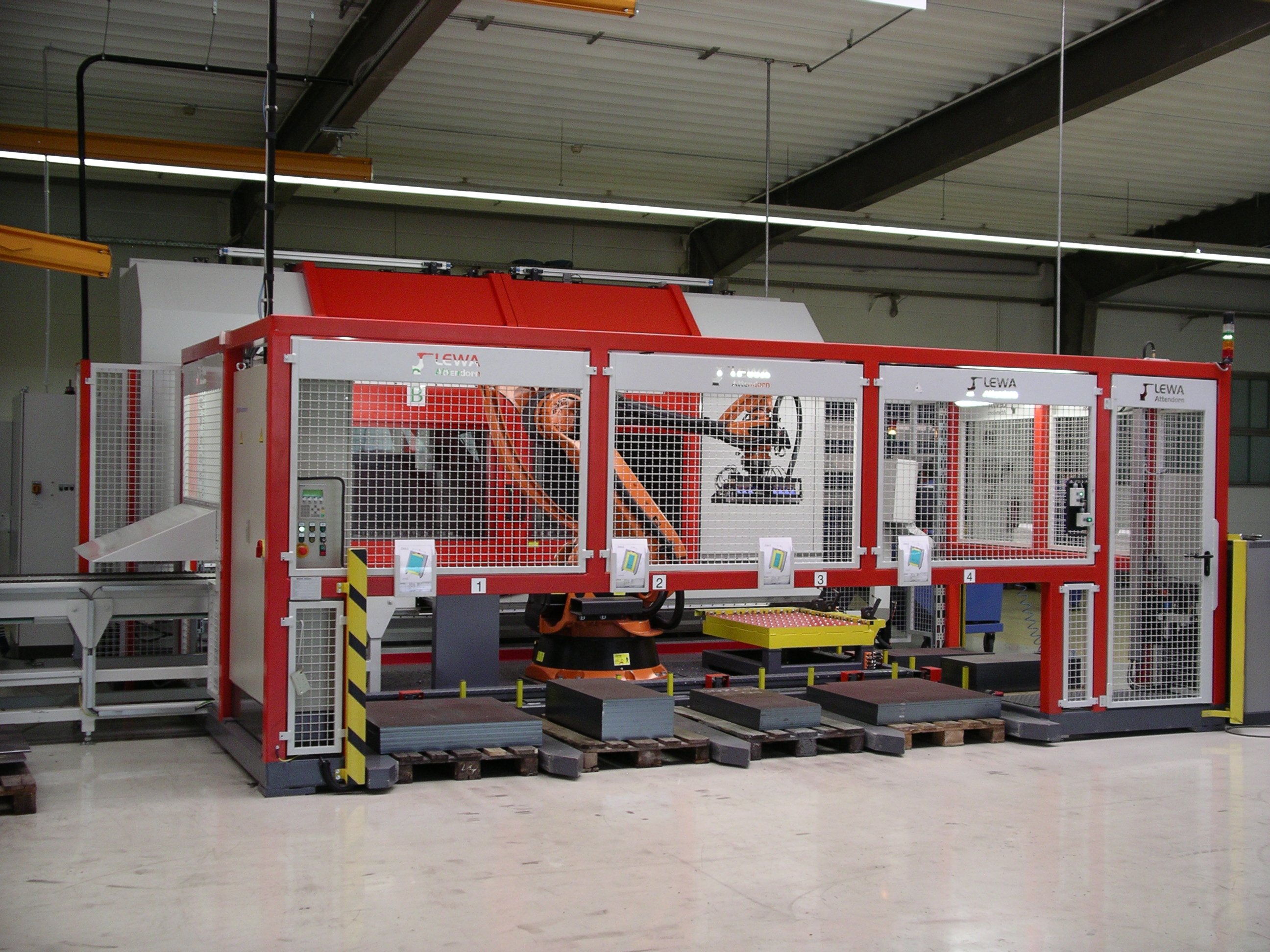
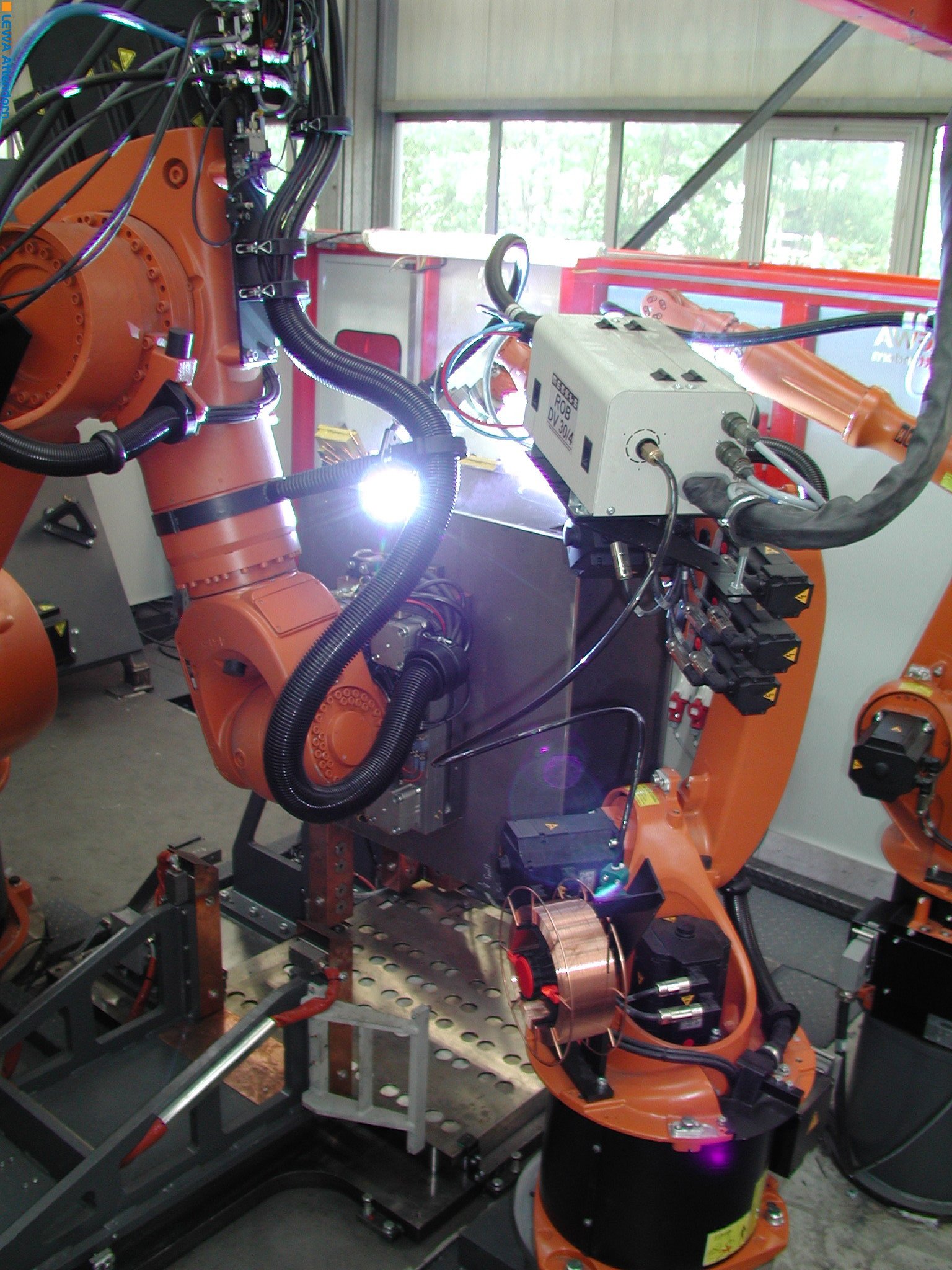
The customer benefit:
Maximum flexibility to a wide range of dimensions and component types.
- Highly automated solution for consistently high quality and productivity
- Several manual operations and transport efforts were replaced via an automation solution
You would like to learn more about LEWA Attendorn? - Sure!
Arrange an initial appointment without obligation and get in touch with us.
