We explain how LEWA Attendorn brings together the highest quality standards, low volumes and a low TCO (Total Cost of ownership) for automation in automotive manufacturing.
Customer requirement:
Concept development of a production system for the rear end of a hybrid super sports car with the highest quality requirements, but in low production volumes.
Application processes:
- Punch riveting (350 pieces per assembly)
- MIG welding (total length 2,480 mm)
- Camera-guided setting of blind rivet studs (48 pieces per assembly)
- Adhesive application including camera control (total length 8,100 mm)
- Sealant application (total length 7,650 mm)
Automation designed for flexibility and ease of reutilization.
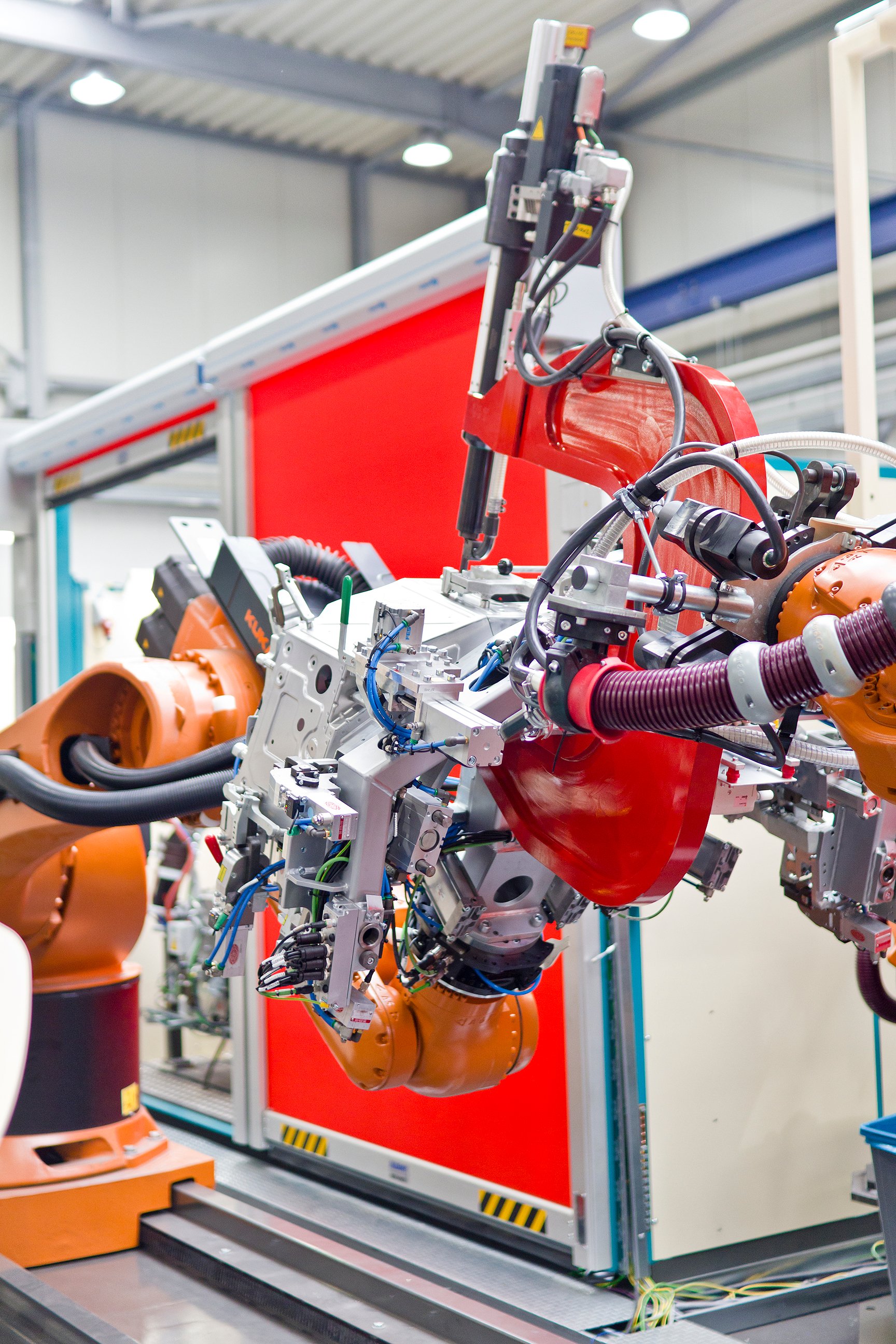
Our solution:
Construction of a highly automated production line from individual, standardized production modules.
- Minimal dedicated tooling through a jig-less process of moving the components to the work.
- Adjustable fixture and gripper technology including an automated change over process for assembly variants.
- Servo-motorized self-pierce riveting technology with automatic tool changers
- Automated adhesive and sealant applications with process monitoring utilizing industrial vision inspection.
- Camera-guided setting of blind rivet studs
- Part marking and documentation of production data
- Discharge of the assemblies in the special load carrier
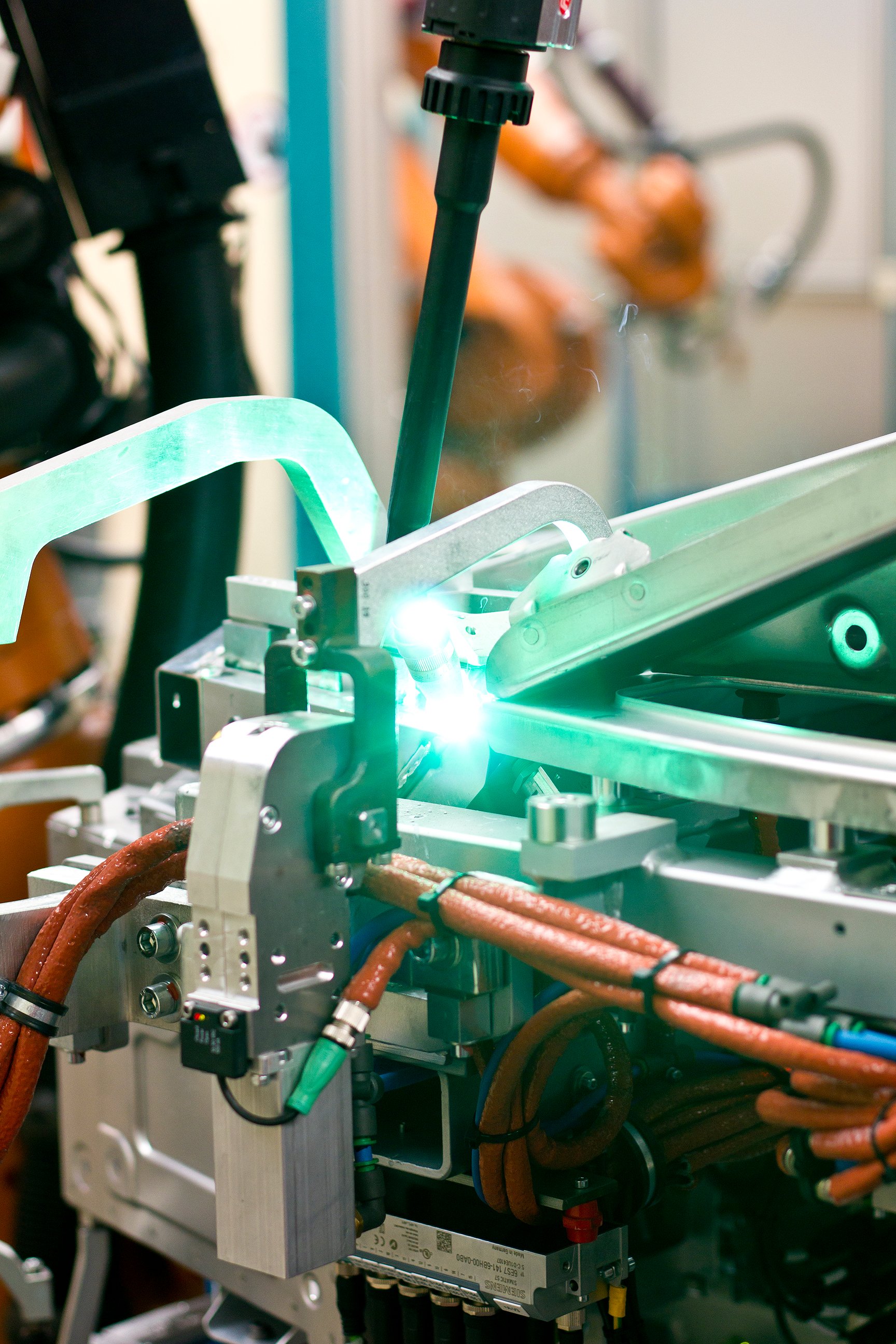
The customer benefit:
Standardized modules that are time tested, reducing costs and speeding up the integration process.
- Flexible production through tooling and fixturing change over
- Modular platform design that simplifies and expedites the relocation of the equipment.
- Concepted and designed with reutilizing in mind.
- Highly automated solution for consistently high quality and consistently high productivity
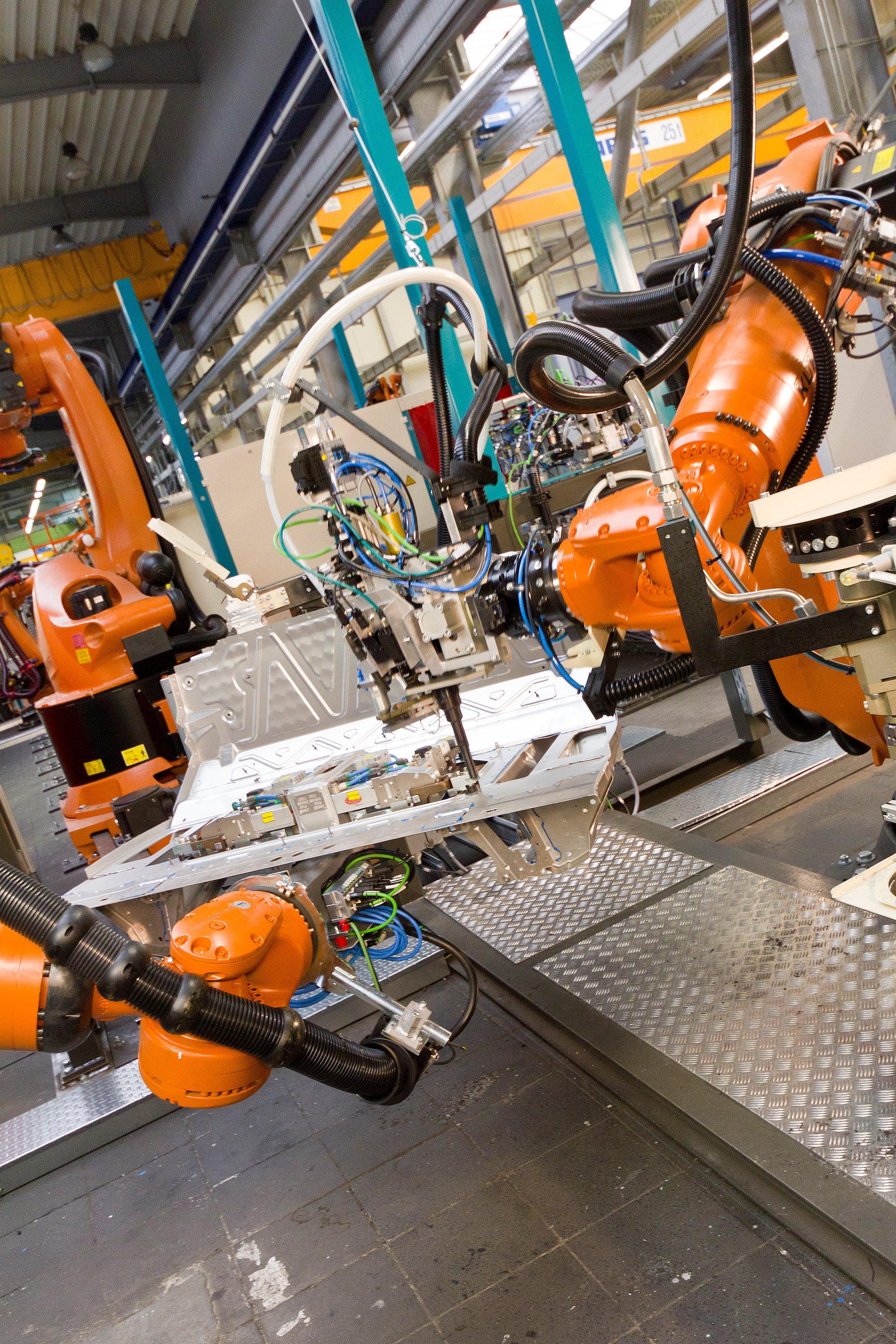
You would like to learn more about LEWA Attendorn? - Sure!
Arrange an introductory meeting or web call with our team to review our capabilites and discuss your automation needs.
