We explain how LEWA Attendorn designed a production system for its customer to manufacture two steel and aluminum rear floor variants.
Customer requirement:
Conceptual design of a production system for the manufacture of two steel/aluminum rear floor variants with planned, staged, volume increases
Application processes:
- Punch rivets (68 pieces/assembly)
- Gluing incl. vision control (number of seams, total length)
- Material handling with customer EOA tooling and dedicated part racks
Our solution:
Construction of a highly automated production line from standardized SpeedLine modules
- Limited operators resulting in greater machine efficiency and through put
- Variable fixture and gripper technology including automated setup process
- Joining by means of servo-driven self-pierce riveting technology
- Automated adhesive application with process monitoring utilizing vision
- Parts marking and documentation of production data
- Stacking of the assemblies in the dedicated racks
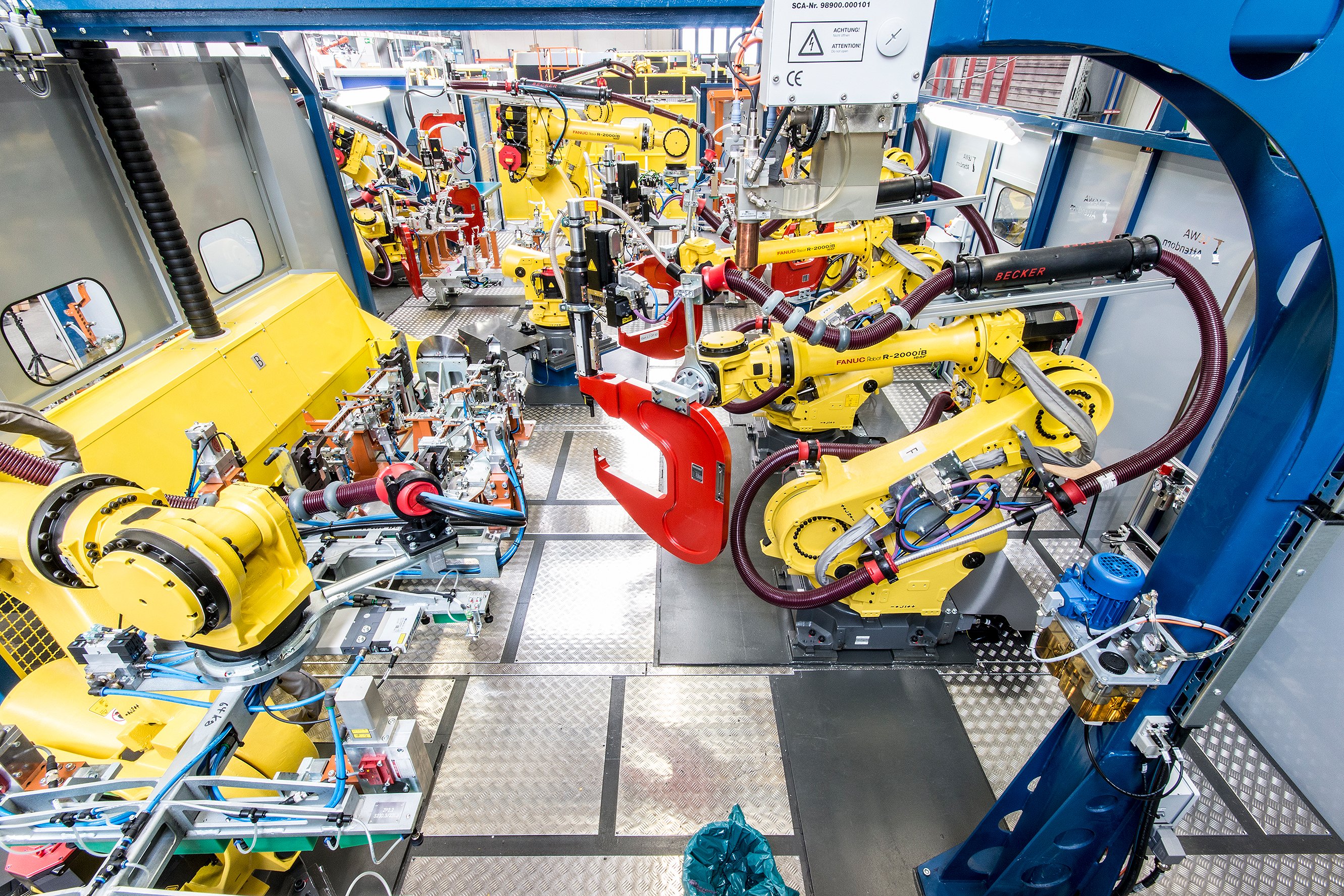
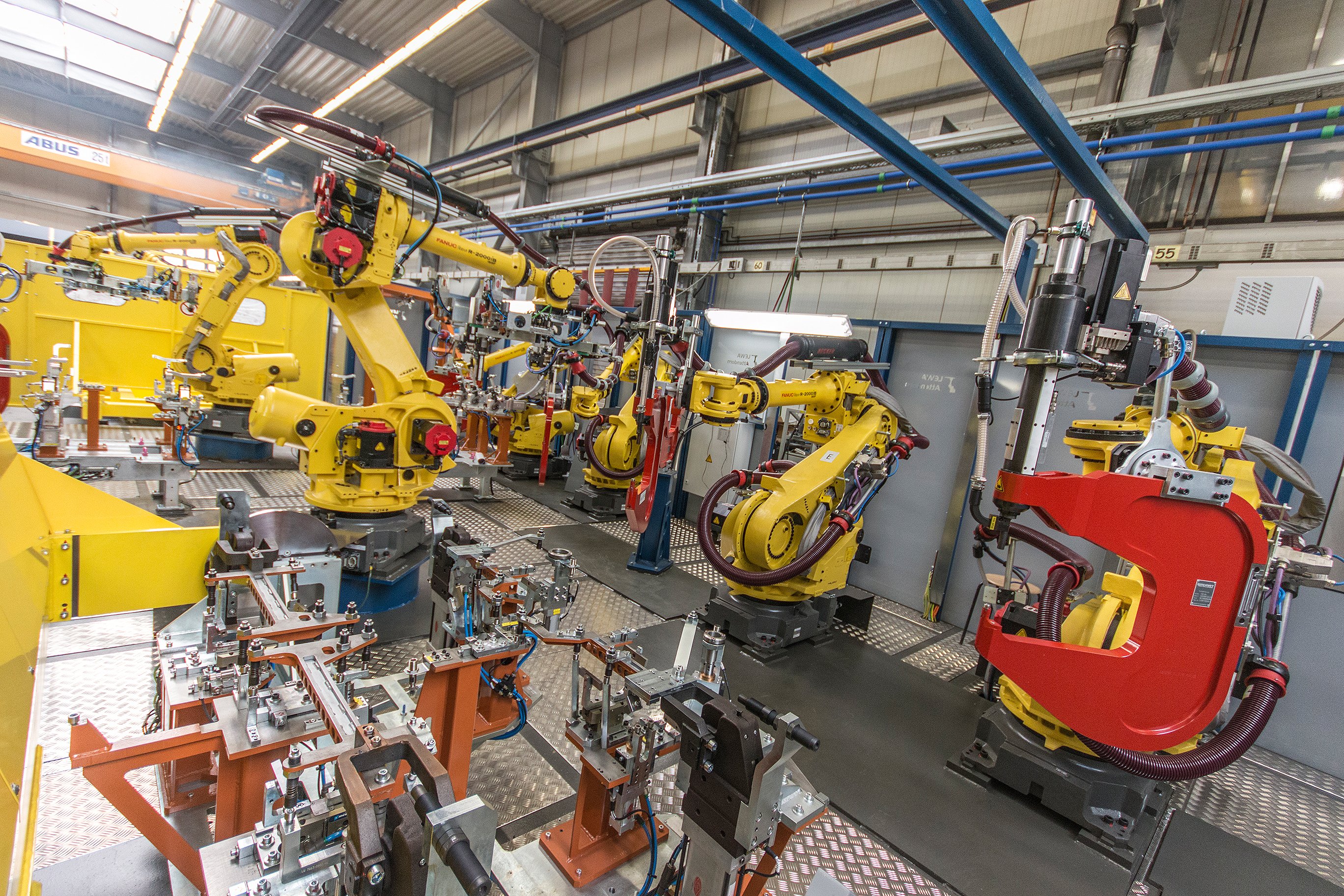
The customer benefit:
SpeedLine standard production modules are characterized by the following advantages:
- Cost-optimized modules that have been successfully used in over 100 production solutions
- Maximum flexibility and can be set up for other products via the tooling technology used
- Scalable to the required capacities (product start-up, peak, product run-out)
- Designed to be relocated very quickly within the company or across the group
- Designed for longevity, flexibility and reutilization for future programs.
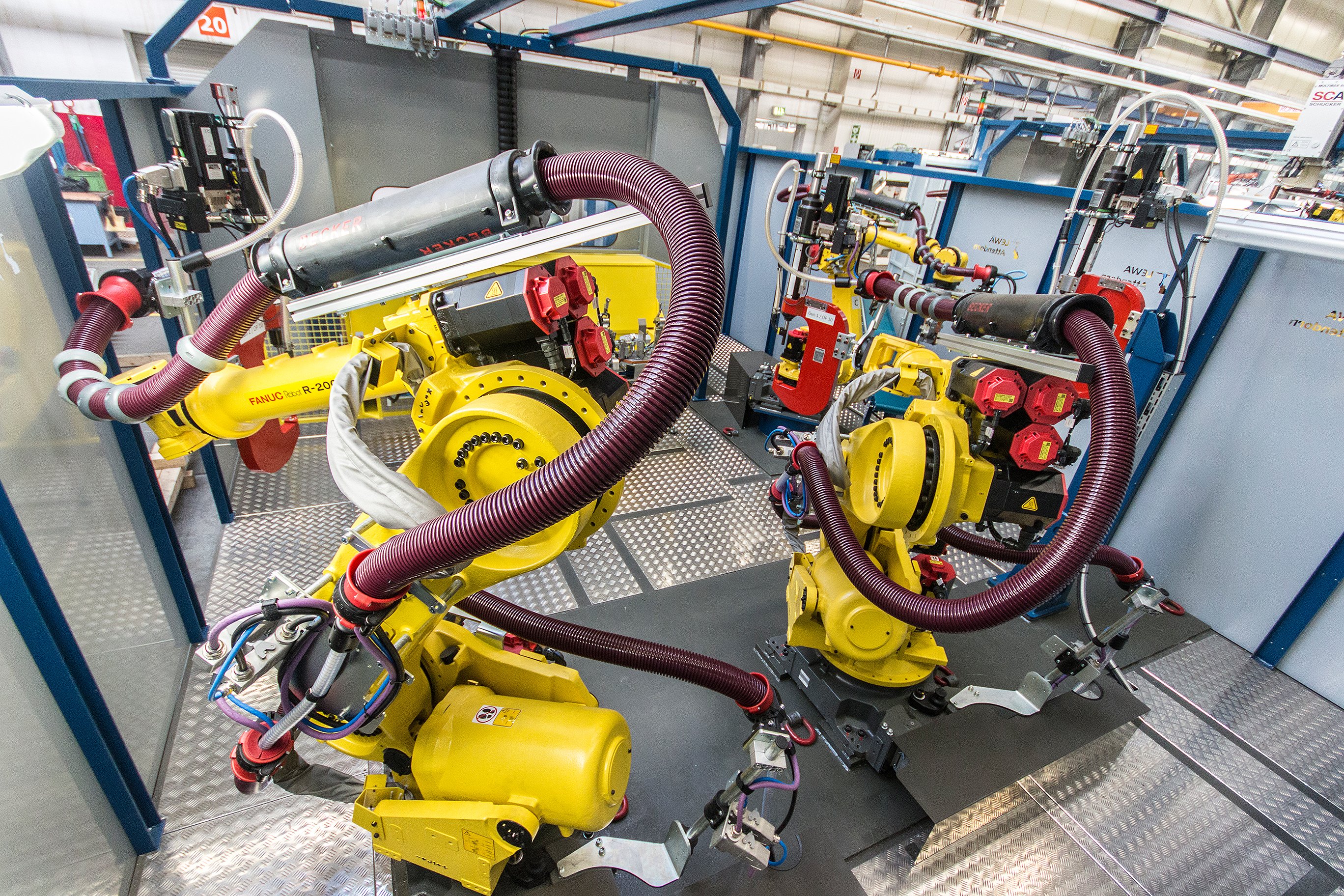
You would like to learn more about LEWA Attendorn? - Sure!
Arrange an initial appointment without obligation and get in touch with us.
