We explain how LEWA Attendorn developed a TURNKEY process solution for the mechanical machining of manual transmission components for its customer.
Customer requirement:
TURNKEY process solutions (stand-alone machining centers incl. peripherals and process) for the mechanical machining (milling & drilling) of manual transmission components while meeting the highest quality requirements and the shortest cycle times.
Our solution:
3 pieces of vertical, 5-axis high-performance machining centers (FANUC Robodrill) with corresponding peripheral components:
- Chip management and coolant supply
- Emulsion / oil mist extraction systems
- tool breakage and wear controls
- Hydraulic media supply for clamping devices
- Component-specific, hydraulic clamping devices incl. air support control (airsensoring)
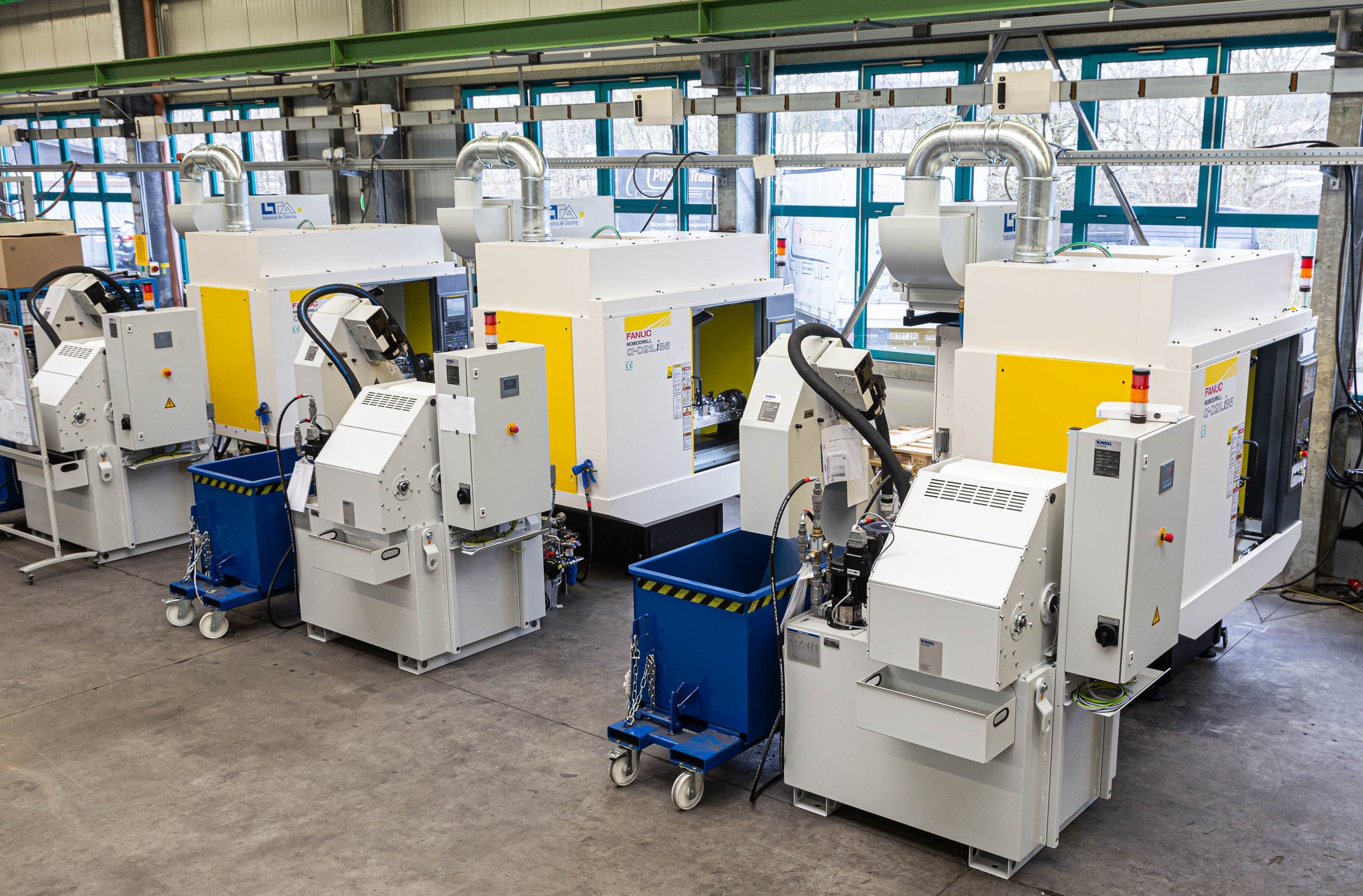
The customer added value:
- cost-optimized and successfully used in series production (24/7) many times over
- maximum flexibility and quick changeover to other components thanks to user-friendly control and fixture technology (KISS principle)
- low personnel requirements due to only one system operator
- can be scaled according to the required production capacity
- are mobile and can be relocated very quickly within the company or within the group (plug and produce principle)
- are designed for several production life cycles and thus also for the possible "reuse" case
- increased system availability / redundancy thanks to high-performance machining centers with their own peripherals
- minimal space requirement
You would like to learn more about LEWA Attendorn? - Sure!
Arrange an initial appointment and get in touch with us.
